Hablemos claro de una vez por todas: gestionar la documentación de Calidad es un tostón insufrible. Hay quien dice que los fabricantes de automóviles crearon APQP o VDA para poder torturar a los proveedores de componentes. Pero seguro que no es así, ¿verdad?
Ahora bien, si uno de mis amigos o un familiar cercano me dijese que pasó el fin de semana repasando un AMFE o revisando Pautas de Inspección, el lunes a primera hora lo llevaría al hospital más cercano para un chequeo a fondo. Allí tienen profesionales que se encargan de ese tipo de trastornos.
Ya sé que me diréis lo importante que es la documentación de calidad como vertebradora del sistema de gestión en una compañía. O como decía la ISO “Escribe lo que haces y haz lo que escribes”. Pero demasiado a menudo, la documentación se convierte en un fin en vez de ser el medio de asegurar procesos capaces de producir piezas a Cero Defectos. Es aquello de que alguien te señala a la Luna y tú te quedas mirando la mano. Y si encima cada fabricante te pide los mismos papeles, pero con distintos nombres y formatos, la tortura se hace completa.
En la filosofía de los referenciales como APQP y VDA hay un aspecto de tipo “contractual”. Si se siguen correctamente todas las fases del proceso de desarrollo y se plasman en la documentación de calidad, el resultado será un buen producto fabricado con un buen proceso. Y al contrario, si tenemos toda la documentación correcta y en orden, seguro que el proceso de fabricación también lo será. Pero compañeros, desafortunadamente no es así y por este motivo el control de Calidad se puede convertir en una tortura.
Hace unos años visité una fábrica para dar una charla sobre ANPQP, el referencial de calidad de la Alianza Nissan- Renault. Tras dar una explicación general sobre el sistema, comentamos cuestiones relacionadas con las dificultades de su aplicación: retrasos en los cronogramas, proveedores sin experiencia y ese tipo de cosas. Pero realmente ese no era lo que más les preocupaba. La pregunta central era: “Fernando, que hacemos si el proveedor se retrasa en la entrega de la documentación”. Mi respuesta fue bastante simple, volver a pedirla. “Pero, que dice en ANPQP si el proveedor se retrasa, ¿Qué podemos hacer?”.
La inquietud no venía por el posible impacto en el proceso, por no disponer de piezas o por que las piezas no sean correctas – La preocupación principal era qué hacer si no llegaban los papeles.
Algunas compañías utilizan la disponibilidad y aprobación de la documentación como un método para AUDITAR el proyecto y confirmar que está finalizado. Esto en principio no me parece mal, pero es muy fácil acabar perdiendo el foco sobre lo fundamental. La documentación de calidad sirve para desarrollar un conocimiento riguroso sobre el producto a desarrollar y el proceso para fabricarlo. Cuando estos dos aspectos estén claros, ya podremos plasmarlo en la documentación.
Llegado este punto, si preguntásemos a los proveedores ¿Cuál debería ser el orden lógico para desarrollar la documentación de calidad?, la respuesta mayoritaria sería: según la fecha en la que te lo pida el cliente. Es una respuesta, pero no la más sensata. Cómo profesional de la calidad, ¿Cuál es el orden lógico en la “creación” de esta documentación?
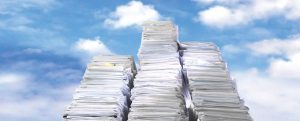
Independientemente de lo que digan los referenciales APQP o ANPQP, mi propuesta es la siguiente:
1er Paso – Qué pieza queremos fabricar ► Analiza tu producto: estudia el plano, el CAD, las piezas con las que interactúa y las normas que le aplican.
2º Paso – Qué queremos controlar ► Ahora que ya sabes que pieza se quiere fabricar, selecciona sus características clave: dimensiones, funcionalidad, aspecto, seguridad, forma de entrega, etc.
3º Paso – Cómo la vamos a medir ► ¿Cómo controlaremos las características clave de la pieza? Define la galga y todas las actividades metrológicas o de control en laboratorio. Y lo más importante, ¿estás seguro de que tienes los recursos materiales y humanos necesarios para realizar los estudios de capacidad?
4º Paso – Cómo es el proceso ► ¿Cuál es el proceso de fabricación que se ha cotizado al cliente? Identifica los flujos del proceso interno, componentes de compra, movimientos logísticos, variabilidad entre referencias – O sea, identifica toda la complejidad del proceso de fabricación
5º Paso – Que podría fallar en el proceso ► Es el momento del AMFE y sobre todo ¿qué problemas han tenido piezas similares anteriormente? No está de más recordar una frase de Einstein “El único error en la vida son las lecciones no aprendidas”. Es súper obvio, pero sin embargo los proveedores repiten errores y defectos similares una y otra vez.
6º Paso – Cómo vamos a controlar nuestro proceso ► Qué controles vamos a ponerle a nuestro proceso, cómo aseguraremos todas las características clave, dónde vamos a colocar los Poka Yoke ¿Será el proceso capaz o deberemos hacer un control 100%? O sea, resume los 6 pasos anteriores en el Plan de Control.
Existen muchos más documentos asociados a la calidad de la pieza, pero si los que he mencionado están desarrollados en profundidad (huye del “corta y pega”) el proceso estará bien asegurado. El control de Calidad se puede convertir en una tortura. Hay más papeles APQP que será necesario rellenar, pero esos ya sólo serán para poder “torturar” un poquito más al sufrido proveedor.
En un próximo artículo podemos revisar cómo la Industria 4.0 nos ofrece soluciones que evitan prácticamente la burocracia, el papeleo y toda esta tortura que suponen los controles de calidad, dejando que suceda simplemente el «control» y la búsqueda de causas raíz para evitarlas.
Otros artículos relacionados: La Calidad empieza por el Taichiai, Cinco maneras (seguras) de arruinar un buen plan, Shoki Ryudo: soluciones japonesas para momentos de crisis