Todo el que haya trabajado en una empresa japonesa sabe que la lista de anécdotas entre las diferentes maneras de trabajar de japoneses y españoles es inacabable. Después de casi tres décadas trabajando en Nissan, una de mis anécdotas favoritas está relacionada con la preparación de los planes.
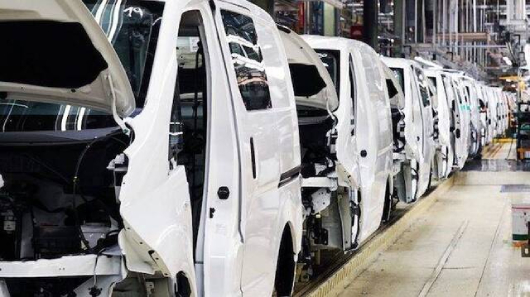
Corría el año 2004, cuando teníamos que preparar una actividad conjunta con proveedores. Durante un par de semanas debíamos hacer el montaje lento de una serie de piezas sobre una carrocería. Al iniciar la actividad, las piezas empezaron a llegar tarde y no por el orden en el que las esperábamos, con lo que toda la actividad se retrasó y sólo la pudimos completar a medias.
Tras esas dos semanas le pregunté al asesor japonés que le había parecido el desarrollo de la actividad. Su única respuesta fue torcer la cabeza y poner cara de póker. “Como sabes – le dije yo – hemos tenido problemas con la llegada de las piezas y eso nos ha roto el plan”. Su respuesta es de aquellas que guardó como un principio fundamental de nuestro negocio “Revilla-san, primero hay que hacer un buen plan y si hay problemas, entonces hay que hacer un plan mejor”.
A menudo y según nuestra mentalidad, la aparición de algún imprevisto es una buena razón para justificar el no cumplimiento de los objetivos marcados. Pero aquellos que trabajamos en lanzar nuevos modelos sabemos que los imprevistos SIEMPRE ocurren.
En aquella época conocí una nueva sistemática de calidad de origen japonés llamada Shoki Ryudo. Podemos traducir Shoki ryudo como “evaluación de la calidad inicial” y su explicación es sencilla – ¿Cómo podemos controlar los imprevistos que seguro nos aparecerán en el lanzamiento de un nueva pieza, vehículo o producto en general?
Cualquier proyecto preparado con esmero durante meses o años, se enfrenta al momento clave en la fase de lanzamiento. Durante la rampa de incremento de producción aparecerán incidencias/ defectos derivados por ejemplo de la formación de los operarios, procesos no completamente validados, parámetros de procesos no ajustados, etc.
El Manual de Calidad dice que la mejor manera de asegurar que estas incidencias no se convierten en reclamaciones del cliente es aplicar un estricto Muro de Calidad, que evite la fuga de defectos. Pero el problema es que si no aplicamos una mejora sistemática de nuestro proceso, el muro de calidad se eternizará con el consiguiente impacto en coste y sobre-gestión. Y además tarde o temprano se fugará algún defecto.
¿Cómo nos ayuda el Shoki ryudo para evitar esta situación? Meses antes de la rampa de producción en serie, definiremos el plan de aseguramiento, que nos permitirá gestionar el muro de calidad. Tenemos que definir y planificar:
¿Quién y cómo inspeccionará las piezas?
¿Quién recopilará la información?
¿Cómo se investigarán los defectos y se aplicarán soluciones rápidas?
¿Qué indicadores vamos a seguir para saber si el proceso falla y dónde está fallando?
Y la pregunta clave, ¿cómo sabremos que podemos retirar el muro de calidad sin tener riesgos de impactar en el cliente?
En todo este camino, la Digitalización de la Calidad es una ayuda fundamental para disponer de la información a tiempo real, resumida y fiable. Tener la información bien ordenada, es el primer paso para tener la solución a los problemas.
En este sentido estuvimos desarrollando un proyecto de colaboración con Kapture.io para la mejora del proceso de gestión de los muros de Calidad. Kapture.io demostró ser una herramienta flexible y adaptable a nuestra necesidad de disponer de la información del muro de calidad de forma inmediata y ordenada. O sea la herramienta ideal para preparar un buen plan y si aparecen imprevistos, hacer un plan mejor.